For over a half-century, Ermak has worked to master and perfect the art of sand mold casting. Sand casting is a popular method of producing non-ferrous alloy casts. This process was invented over 6,000 years ago and continues to undergo modernization. There are three types of sand used in casting, green sand, water glass or sodium silicate, and resin sand.
Over 70% of the world’s metal castings are produced via the sand-casting process. Sand casting is highly efficient and cost-effective.
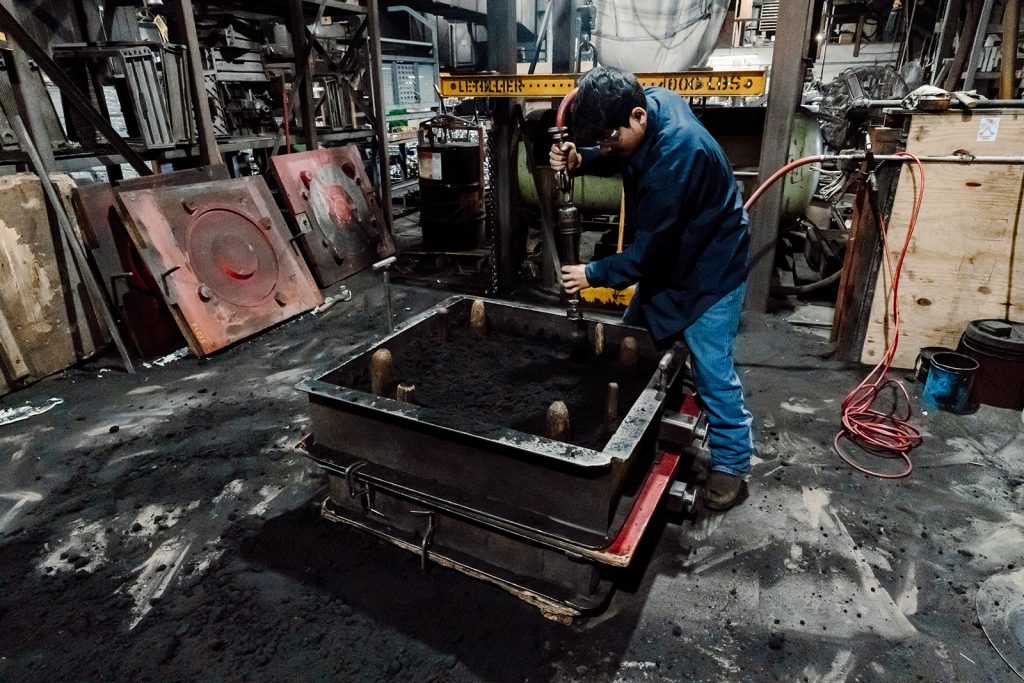
Types of Sand Used in Sandcasting
1. Green Sand
Green sand castings are formed using sand molds formed from wet sand that contains water and organic bonding compounds, also known as clay. The term Green Sand refers to the sand mold not being “set” or “green” or “uncured” when the metal is poured into the mold. Because the sand can be reused, sand casting with green sand is easy and inexpensive. The disadvantage is that sand is a soft mold that can collapse or shift during casting.
2. Water Glass or Sodium Silicate
Sodium silicate can be used to create sand mold castings. This process is beneficial in sand casting, where a cavity is required. Sodium Silicate can quickly go from a liquid to a solid by passing carbon dioxide through it. This causes the sodium silicate to dehydrate. Sodium silicate must be mixed with other materials so the core can be removed during product break down. If the mixture isn’t correct, the core will become stuck within the casting.
3. Resin Sand
The molding material for resin sand casting is a blend of quartz sand and resin sand. When resin sand is mixed and heated, it hardens into a solid, smooth mold. A solid mold produces fewer faulty castings, but it comes at a greater cost and a slower production rate. Resin sand molds take longer to make because each one must be mixed and burned individually.
2 thoughts on “3 Types of Sand Casting”
Awesome that the green sand molds are 99% recyclable! Are they a one-time use mold? Or can they be used for several pours?
Thanks! The sand foundry industry is one of the highest ranked for percent of material recycled. In this case, we make a new sand mold for each product. Once the molten metal is poured into it, we then let the product solidify, the sand cool and then prep the sand back to “like new” condition to make another mold.
Comments are closed.