We often hear from customers looking to create a prototype part in order to test it, physically check it for fitment, and/or get customer feedback. Typically, the parts are requested to either be machined from bar stock or billet aluminum. While this is feasible, it tends to be expensive to complete the programming and time consuming to setup the CNC, especially when it is only a few parts. What customers are much more surprised to hear is that we can make prototype castings in a number of different ways, typically with fast turnaround times and substantially lower cost than sample machined parts.
There are two main ways of getting a prototype or very low run production castings. The first is to take a 3D printed plastic part that has been modified to include draft and adjustments for metal shrinkage. Then we run through it through our proprietary sand prototype process. After the first review we either help the customer adjust the 3D model to be printed or have them printed ourselves, then turn the part around in as little as a few days. If secondary processes are required (machining, heat treating, painting), it will typically add a week or two to the process. The cost ranges from $50-200/part depending on the size and any secondary finishings, and is “95%” of a production part, with minor differences in surface finish and quality.
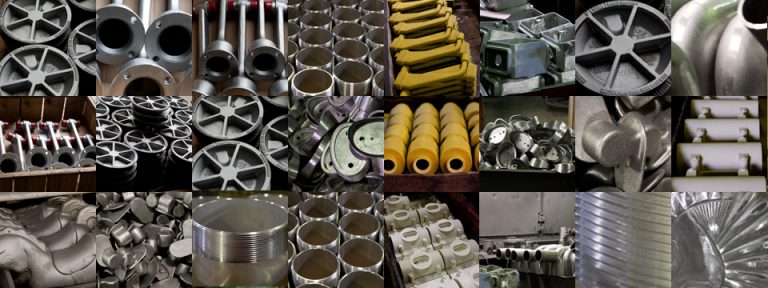
The second way we build prototypes is to work with third party partners who will 3D print sand patterns for us, similar to the way production sand patterns work. Once the CAD file is adapted for shrink and draft, we typically get these patterns in-house in a few weeks and parts poured in as little as a few days (minus any secondary finishing required as noted above). Normally, this process will cost $250-1000/part depending on the size/complexity and it will be “99%” of a final part, nearly identical to what we will create during production.
Some customers don’t have a 3D CAD file, they only have a sample of a part or a simple sketch. At this point, we are able to either create a part directly from the sample (say of an old car part) that will be ~1-2% smaller than the original part or we can create a 3D CAD file that the customer approves. The 3D file can be from scratch or by completing a 3D scan of the part, whatever is needed we are able to take care of. From this CAD file, we can then run through the first process outlined above.
Share your experiences on prototyping or reach out to us for how we can help develop your first part! Free quotes and advice, info@ermak.com or (952) 448-2801.