For thousands of years, non-ferrous metals have played a part in human innovation.
The first metals used by humans were non-ferrous. The use of bronze, a copper and tin alloy, signaled humankind’s transition from the Stone Age to the Bronze Age, around 3200 BCE. Non-ferrous metal casting is one of the most influential industrial methods in the world. For the last thousands of years, the techniques and procedures have been updated and improved, but the basic theory is timeless and has allowed for continued innovation.
Non-ferrous castings are critical for today’s industries’ which demand exact regulations, standards, and quality. The 21st century automotive, energy/power generation, medical technologies, military/defense, fluid handling and plumbing, industrial, marine, tooling and machinery, housing, construction, and aerospace industries all require their products to be made from the right alloy using precision manufacturing procedures. Non-ferrous metal castings are renowned for their superior durability, product characteristics, and high-performance levels.
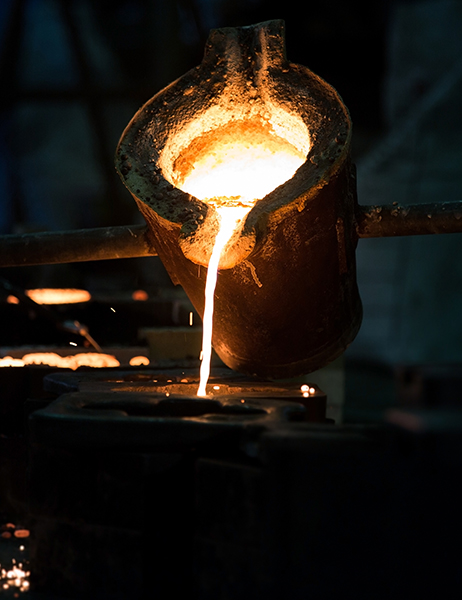
What are Non-ferrous Metals?
Non-ferrous metals are chemical compounds found on earth. All pure metals are non-ferrous elements except iron. Non-ferrous metals cover a wide variety of metals or alloys. Most of what we call metals today are more accurately called alloys. True metals are pure elements, while alloys are blends of two or more metals that have been melted together. Alloys are made by mixing two or more elements, at least one of which is a metal. Combining alloys is a skilled balancing act that produces huge benefits. Well-controlled alloys produce highly desirable properties.
Commonly recognized metals include, aluminum, lead, tin, zinc, nickle and copper. Non-ferrous copper-based alloys include brass (an alloy of copper and zinc) and bronze (an alloy of copper and tin). Precious metals like gold, silver, and platinum also fall into the non-ferrous category.
What are Ferrous Metals?
Latin ferrum, means “iron” or ferrous metal. Most ferrous metals have magnetic properties. So, if a magnet sticks to your metal, it contains iron, which also means it is ferrous metal. If the magnet is not drawn to the metal, it does not contain iron because it is non-ferrous. Iron and steel, prized for their durability and tensile strength are traditionally used to construct bridges, railroads and skyscrapers.
Why Use Non-ferrous Metals?
Reliability, versatility, workability, and price are among the many reasons industries choose non-ferrous alloys. Attributes of non-ferrous metals:
- A high strength-to-density ratio
- Corrosion-resistance
- Lightweight
- Highly conductivity
- Malleability
- Non-magnetic properties
Ermak can help guide your alloy selection process as you consider workable options for products where friction, wear, and corrosion-resistance are factors.
Non-ferrous alloys allow for endless product possibilities
Numerous products can be made using non-ferrous casting methods. With so many non-ferrous alloys available to work with, these metals can be used for almost endless applications. Here’s a tiny sample.
- Boat, sailboat and dock hardware
- Transportation
- Infrastructure
- Outdoor sports and recreation equipment
- Agriculture parts
- Automotive and racing
- Explosion and fireproof equipment
- Hydraulics
- Food equipment
- Electronics and appliance framework
- Brackets, flanges, housings, sheaves, gears, pulleys, and wheels…
Non-ferrous Metal Alloy Casting Process
Preliminary Non-ferrous Casting Services
Our non-ferrous casting services provide a number of preliminary measures to guarantee that you not only get custom castings but also exactly what you need to develop your product.
- Assembly Analysis and Casting Integration – Determine ways to minimize costs prior to casting assembly.
- Reverse Engineering– Replicate castings that have been produced elsewhere using standard CAD software (typically SolidWorks). Analyze and identify non-ferrous metals.
- Non-Ferrous Prototypes – Producing casting prototypes, both completely usable and non-working, for use in presenting to test markets, stakeholders, or other primary decision-makers.
Existing Casting Process
- Pattern/Die Details
- Cores
- Quantities
- Weight & Dimensions
- Existing Tooling
- New Tooling
- Tooling Changes
- Manufacturability
- Optimization
- Pattern/Die
- Machine Part Holding
- Provide Parts
- Discuss Results
- Modify as Needed
- Standard Lead Time
- Expedites as Needed
- Inventory Discussions
- Cost/Lead Time Improvement
- Quality Improvement
- Weekly Update Open Orders
New Casting Process
- Designs/DWG’s
- Application Qualities
- Budget
- Timeline
- Tolerances/Specs
- Casting Process
- Lead Time
- Price Trade-offs
- Manufacturing Process
- 3D Plastic
- 3D Sand
- Machine
- Welded Part
- Machine Part Holding
- Provide Parts
- Discuss Results
- Modify as Needed
- Standard Lead Time
- Expedites as Needed
- Inventory Discussions
- Cost/Lead Time Improvement
- Quality Improvement
- Weekly Update Open Orders
Non-ferrous Casting Processes
Metal casting is a complicated process that involves pouring liquid metal into a mold, allowing it to cool, and then extracting the product. Depending on the metal used and the required outcome, we’ll use either sand casting or permanent mold casting.
Non-ferrous sand casting is highly efficient and cost-effective.
- Green Sand Casting: sand is squeezed into two halves around a pattern. The pattern is removed. The sand is then pressed together, and molten metal is poured into the negative imprint of the part in the sand.
- Air Set Casting (no bake): typically used for larger castings with complex configurations.
Permanent mold also referred to as gravity-fed die casting utilizes gravity when pouring molten aluminum into molds (or dies) machined from cast iron or steel.
Aluminum, Bronze and Zinc-based Alloys
At Ermak Foundry & Machining, our aluminum metal casting process consists of melting down alloys. We use certified aluminum ingot—319, 333, 356, A356, 535, and 713 – and accommodate flask sizes from 12″ x 14″ up to 60″ x 60″. With the acquisition of Patriot Foundry & Castings, we now offer an expansive range of aluminum, brass, bronze, zinc, and other copper-based alloys.
Ermak Foundry & Machining takes pride in producing high-quality castings that are consistent, repeatable, and cost-effective. We customize the process to meet your needs using the best, most efficient non-ferrous metal casting process for your product. For additional information about our casting services, please contact us to learn more!