FINISHING
Surface finishing requirements depend on a product's application.
Our finishing process includes taking cooled, molded cast assemblies and preparing them for use. Castings are separated from the gating/risers, and all flash and parting line metal is removed.
Depending on the casting type (air set/no-bake, green sand, or perm mold/gravity-fed die-cast), finishing may involve several steps. Often heat treatment provides better surface finishes, improves machinability, and strengthens mechanical properties.
We start the finishing process by grinding unfinished edges from coarse to fine, then we polish, continue to grind, and shot blast until the castings are at the desired finish.
Our surface finish provides an excellent base for secondary processing such as additional machining, heat treating, plating, powder coating, zinc plating, anodizing, or traditional wet painting.
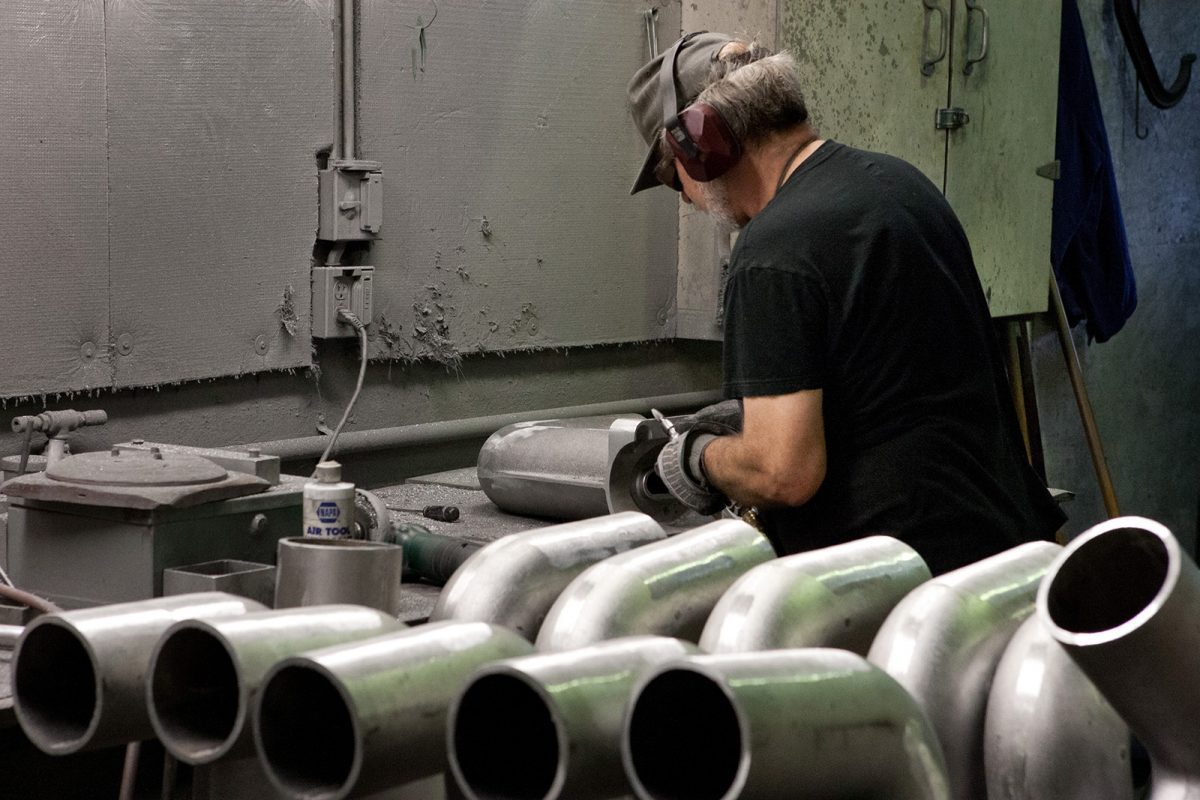
When is surface finishing needed?
- To enhance a product’s appearance and aesthetic features, to make the product more attractive and appealing,
- To protect the product from dirt and corrosion, UV rays, water, fungus, and chemicals,
- To strengthen the product to make it more durable,
- To hide tiny flaws that emerged throughout the production process,
- To improve the surface qualities of the product in some way.