Benefits of Aluminum Prototype Casting
- Designers/engineers can gain tangible proof of the component’s quality, find unexpected flaws and perform testing that delivers invaluable data.
- Marketers can use prototypes to gain feedback from customers or investors before full-scale production begins.
- Designers/engineers can make parts in a wide range of sizes and surface details with various finishes.
- Designers can cast unique artistic or decorative sculptures, products, or objects.
- Casting is often the cheapest and most direct way of producing a prototype.
- Easily produce complex shapes.
- Cast almost any sort of product.
- Produce almost any size of casting.
- Reduce a product’s development timeline.
- Allow for functional and product performance testing.
- Allow for low-volume, short-run production without the need for expensive tooling.
- Reduce development costs to improve return on investment.
- Create a wide range of products or custom accessories.
The Fundamentals of Prototype Casting
A prototype is a first model of an object that may be used to generate or duplicate further forms. Mold casting is one of the techniques used by engineers and manufacturing professionals to create prototypes.
Casting is a manufacturing method in which a liquid substance is poured into a mold with a holed-out negative impression of the required shape and subsequently solidified. The solidified part, called a casting, is discharged/broken out of the mold to complete the process.
The Basics of Casting
- Melt the metal
- Pour metal into a mold that has already been created and conforms to the shape of the intended component
- Allow the molten metal in the mold to cool and solidify
- Remove the hardened piece from the mold, clean, and, if necessary, apply further finishing and treatment
3D Modeling
3D modeling is an alternative to prototype casting. 3D modeling is a process that produces a three-dimensional physical object from a digital printer by laying down many successive thin layers of material. Although 3D modeling appears to have infinite potential, it does have some restrictions.
The layers of material in a 3D print are constructed on top of one other but not fully fused, resulting in a prototype that closely but may not perfectly reflect the object’s real strength and shape. Limited mediums, differing accuracy, manufacturing constraints, size and durability difficulties are all issues that the 3D printing process may face depending on the part and material used.
There is an alternative to 3D modeling/casting where an ABS/PLA-type material is printed and then used in place of a pattern. The process has some limitations when hollowed-out shapes are required, but for some applications it creates a fast and inexpensive method to get a part.
3D Printed Sand Patterns
3D sand printers are similar to the 3D printed models, except they print the negative impression of the part. We work with third party partners who 3D print sand patterns for us, similar to the way production sand patterns work. Once the CAD file is adapted for shrink and draft, we typically get these patterns in-house in a few weeks and parts poured in as little as a few days (minus any secondary finishing required). Normally, this process will cost $250-1000/part depending on the size/complexity and it will be “99%” of a final part, nearly identical to what we will create during production.
Create Part from Sample
Some customers don’t have a 3D CAD file, they only have a sample of a part or a simple sketch. At this point, we are able to either create a part directly from the sample (say of an old car part) that will be ~1-2% smaller than the original part or we can create a 3D CAD file that the customer approves. The 3D file can be from scratch or by completing a 3D scan of the part – whatever is needed we are able to take care of it. From this CAD file, we can then run through the any of the processes outlined above.
Share your experiences on prototyping or reach out to us for how we can help develop your first part! Free quotes and advice at info@ermak.com or (952) 448-2801.
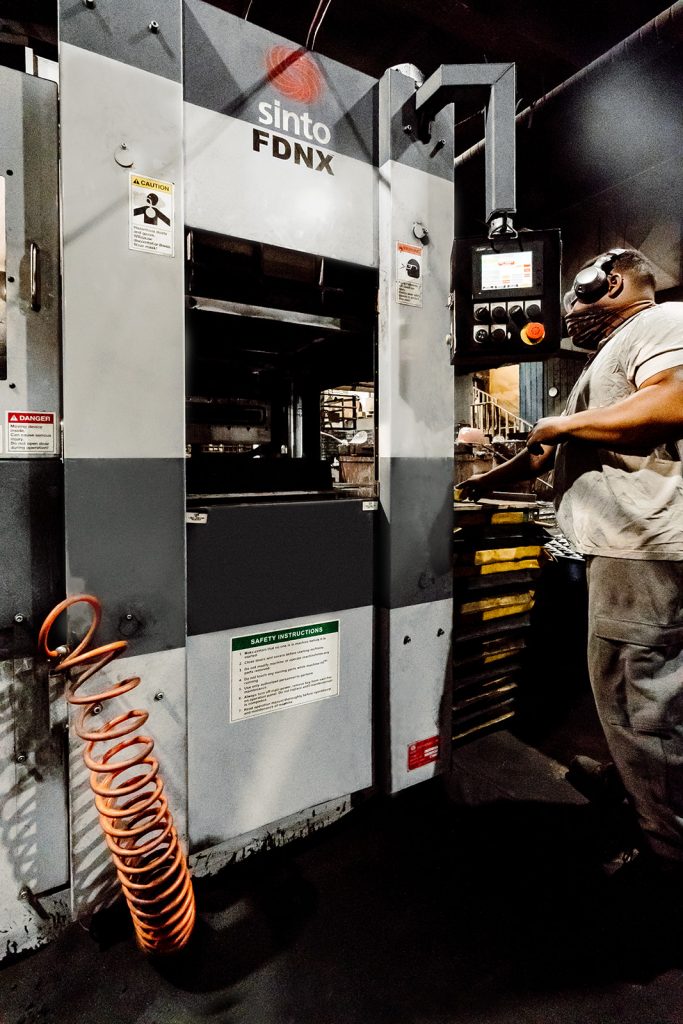
More About Prototypes
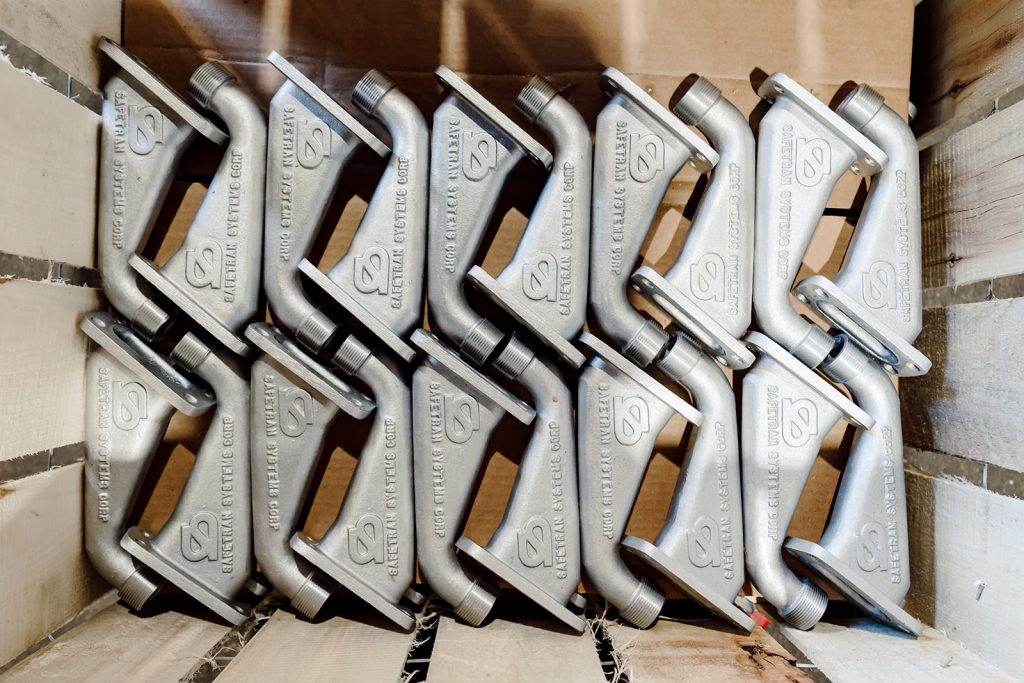