Lightweight, durable and highly recyclable, aluminum is a sustainable material of choice. Aluminum applications span from everyday items like fuel-efficient vehicles to smart phones to window frames to airplanes. It has a long list of inherent assets that makes it referred to as a “miracle metal” – lightweight, corrosion resistant, easily formed, highly conductive, highly reflective, non-toxic, durable and recyclable – and gives manufacturers and designers a wide range of options for product innovation and process improvements.
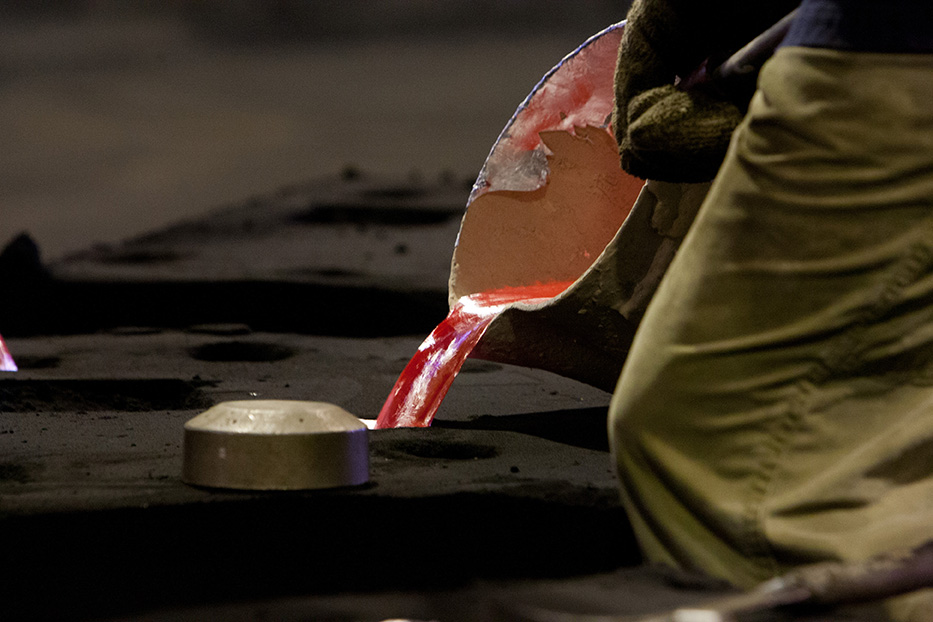
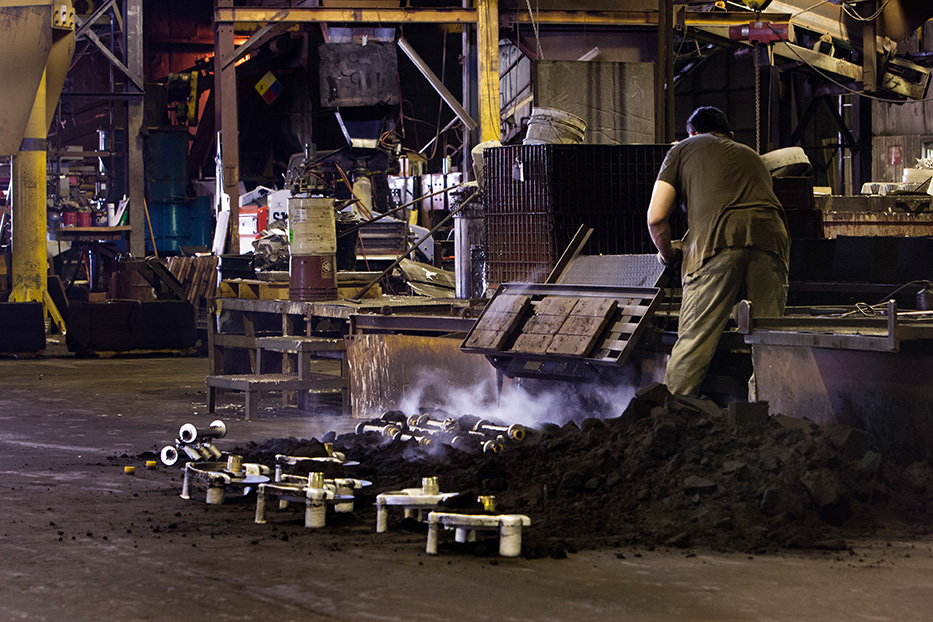
Three of the most common methods for pouring aluminum castings are high-pressure die casting, permanent mold casting (or gravity-fed die casting) and sand casting (typically green sand or air set/no-bake).
- Die casting process forces molten aluminum into a steel die (mold) under pressure. This manufacturing technique is normally used for high-volume production (hundreds of thousands of parts per year) and has start-up costs in the high tens of thousands to hundreds of thousands of dollars in tooling.
- Permanent mold/gravity fed die casting involves molds and cores of steel or other metal, and molten aluminum is poured into the mold until it cools. Traditionally utilized in higher quantity manufacturing runs (tens of thousands of parts per year) or when as-cast tolerances, surface finish, or quality are a key requirement.
- Sand casting utilizes a fine sand mixture to press onto a pattern to form the mold into which the aluminum is poured. Sand casting is a slower process, but usually more economical for smaller quantities (one to tens of thousands), intricate designs or when a very large casting is required. Typically, start-up costs are 4-10x less than perm mold or high pressure die cast, and change-outs from one product to the next takes minutes, rather than the hours sometimes required for other methods, so very low volumes are feasible.
To learn more about aluminum check out the Aluminum-Association
Reach out to our experts at Ermak for free quotes and advice.